When defining, managing and monitoring a health programme applied to rodent animal facilities, the objective is to reach and maintain and defined health standard, more or less demanding. The health standard is defined according to the species, the strain / stock, the use of animals and research applications… The definition is based, at least, on an exclusion list defining microorganisms and parasites which must be excluded from the animal colony, leading to a various level of stringency both for Specific Pathogen Free (SPF) or Specific and Opportunistic Pathogen Free (SOP) colonies. In a increasing number of cases, this “negative” definition is extended to a “positive” one, defining the microbiota which has to be implanted and maintained (gnotoxenic rodents).
In all cases, the main monitoring methods and success indicators are based on the screening for the presence and / or absence of all defined biological agents.
Such rodent colonies must be maintained and used in “barrier rooms” and or in “bioexclusion” housing / caging equipment allowing to maintain the expected health standard. Numerous barriers and practices are used to achieve this objective. One of them is air filtration at different levels: room, housing / caging equipment (isolators, static filter top or IVC cages, cabinets) and handling / procedure equipment (laminar flow or biosafety cabinets). As a consequence, controlling air quality and filtration is one of the key components of the health management programme. This document aims at providing general and basic information about standards related to air quality and filtration.
Of course, in animal facilities, the level of airborne particles is not an issue as they are constantly generated by animals (hair loss and desquamation) as well as by feed and bedding (generation of particles and dust).
Clean rooms and air quality standards
A clean room is an enclosed space in which airborne particulates, contaminants, and pollutants are kept under control, within defined limits. They are used in industry for the manufacture of electronic components (such as integrated circuits or hard drives), vaccines or pharmaceutical / biotech products. The goal is to ensure that the environment is free from contaminating particles, inert or living (bacteria, viruses, or other microorganisms). In addition, temperature and humidity is generally controlled.
Clean room specifications for particulate matter are defined according to the maximum allowable particle diameter and to the maximum allowable number of particles per unit volume (cubic meters or cubic feet). In this context, clean room operation is based on four basic principles:
- Contaminants must not be introduced from the outside into the controlled environment;
- The equipment / activities in the clean room must not generate or give rise to contaminants;
- Contaminants must not get accumulated in the controlled environment
- Existing contaminants must be eliminated rapidly and to the greatest extent possible.
The main applicable international standard is ISO 14644-1:2015. It specifies the classification of air cleanliness in terms of concentration of airborne particles. ISO Class 1 is the most demanding level, and ISO Class 9 the less demanding.
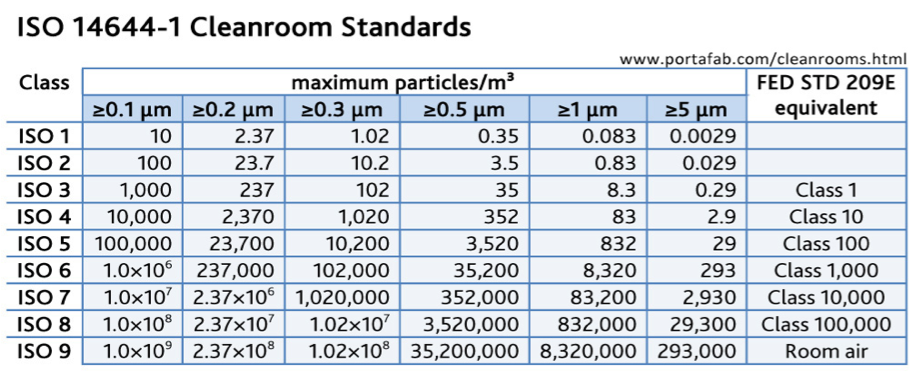
Other classifications are used, such as the EU GMP guidelines, which are applicable to pharmaceutical manufacturing and are more stringent than others, requiring clean rooms to meet particle counts at operation, i.e. during manufacturing process and at rest, i.e. when manufacturing process is not carried out but room ventilation is on.
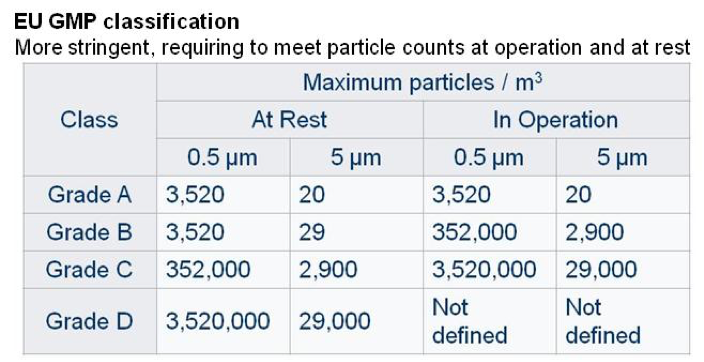
These classes can be used in combination to define the expected efficiency at laminar air flow level and at clean room level. As an example a specific manufacturing step could be conducted in a laminar air flow cabinet (grade A class) placed in a clean room (grade B class).
Air filtration standards
In Europe, HEPA and other high efficiency filters are subject to classification according to European Norm EN 1822 defining filtration efficiency and absence of leakage. It requires declaring the efficiency of the filter tested on the most penetrating particle size (MPPS). HEPA filters are also subject to individual tests. The international standard ISO 29463 is based on EN 1822 standard and will probably replace it in the future. These standards are based on the latest particle counting methods.
The table below illustrates various filtration levels (including HEPA H13 and H14).
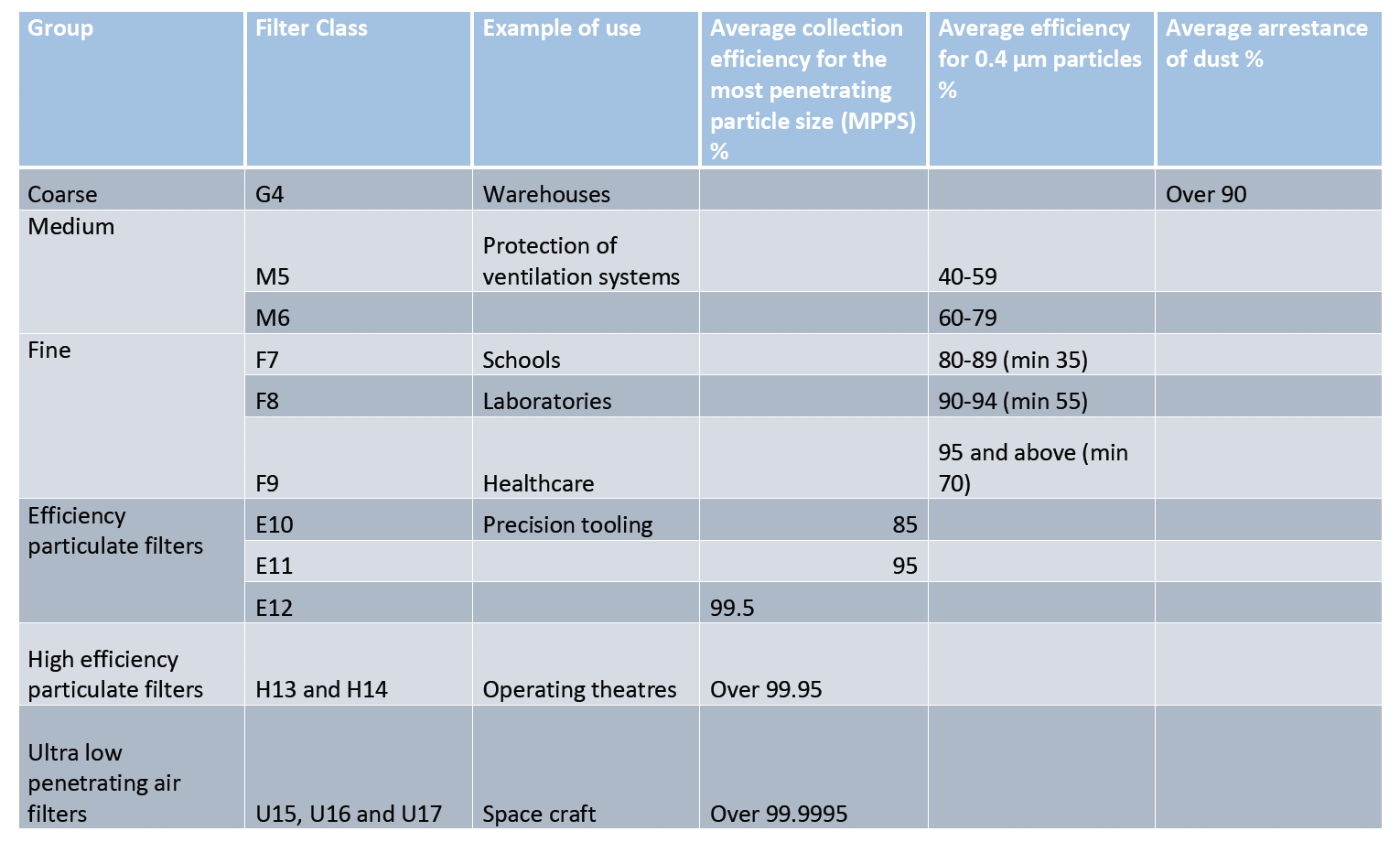
The table below illustrates the size of different particle categories.
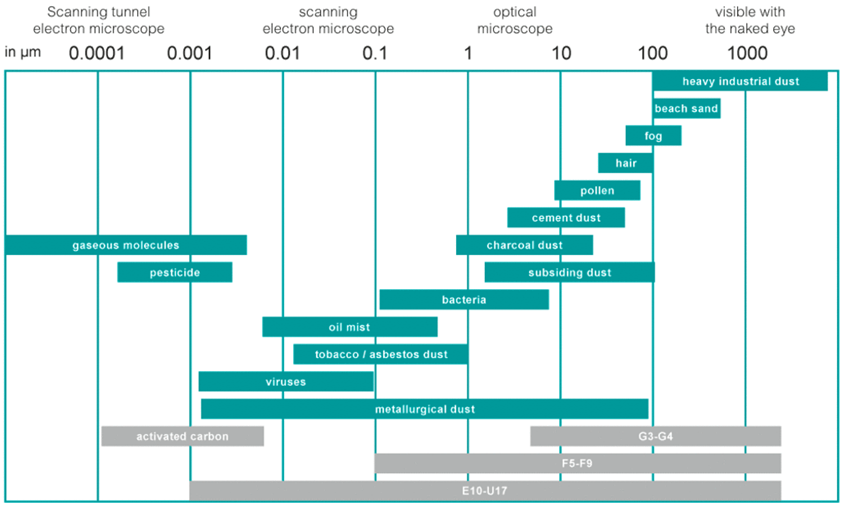