Everyone faces challenges in the workplace. And overcoming these challenges might seem daunting at first. But there’s good news, David W. Brammer, DVM, DACLAM, discusses opportunities to conquer these barriers in our Webinar, “Continuous Improvement in the Lab Animal Field,” to help your lab animal facility thrive.
So, have you personally dealt with discouraged staff, an endless list of unobtainable tasks, or just tons of clutter and chaos? Here’s a comprehensive list of Brammer’s tips, in phases, to improve your lab animal facility to obtain cleanliness, order, and peace. With more organization comes more productivity and success.
Use Effective Organization Tools in Your Lab Animal Facility
Do you have specific programs to encourage your team to focus on organization? If not, it’s something worth considering. Brammer discusses two tools he uses at the University of Houston to stay organized, the 5S’s program and visual workplace tools. He explains how consistently implementing these tools makes them more effective.
5s Program
The 5S program is a scoring sheet that Brammer uses at the University of Houston to teach and guide staff to work neatly. The 5S’s focus on five phases of organization: sort, straighten, shine, standardize and sustain.
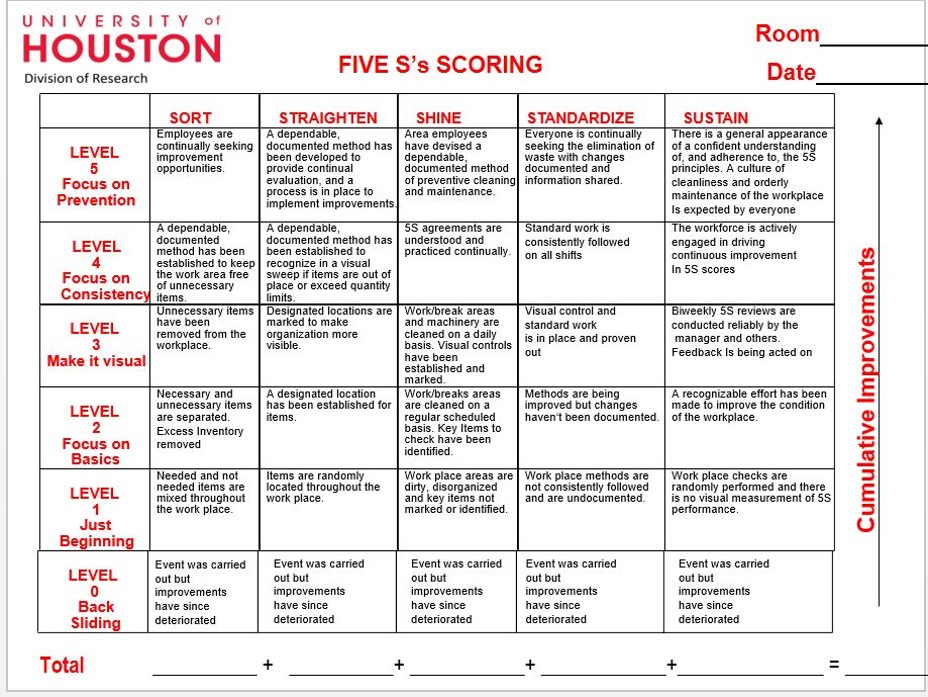
Brammer emphasizes the importance of tackling these steps in order, one at a time. For example, he highlights the importance of the sorting phase. Brammer explains how many people jump right to the straighten phase before they sort anything out. He urges that by skipping this step, you could be setting yourself up for failure.
Mastering the Sorting Phase
When you’re sorting items in your facility, Brammer recommends you ask yourself these three questions:
- What is here?
- What needs to stay here?
- How can I use it in this location?
Answering these questions is fundamental for efficiently beginning to sort through your facility. Furthermore, Brammer recommends a system for answering these questions, the corner-to-corner strategy. Basically, it entails scanning each item in a room, from one corner to the next, and asking yourself: does this belong here? This way, nothing gets forgotten.
Visual Workplace Tools Can Help Your Lab Animal Facility Thrive
Additionally, Brammer recommends using visual workplace tools to teach, guide, and maintain standards. At the University of Houston, Brammer’s team has visual workplace tools posted by various machines that technicians can refer to as they work.
Brammer explains that for visual workplace tools to be most beneficial, they must include clear directions, be appealing to look at, and most importantly, show operators how their end goal should look. When team members have a precise understanding of what their end goal is, they are more successful.
Advice to Keep Visual Display Tools Up to Date
A common issue in any facility is the oversaturation of visual workplace tools. For example, if you have too many posters hanging everywhere, they tend to blend in rather than stand out.
As a result, Brammer recommends hosting a “take down the sign day.” He verifies that setting aside time to take down old signs is just one simple practice that can help ensure your facility’s signs are up to date. So, choose a day to walk through your facility and take down visual display tools that are no longer relevant to your operation.
Standardizing Your Facility’s Daily Operations Can Help Your Lab Animal Facility Thrive
Brammer explains that once you create a solid base in your facility with organizational tools, you can effectively begin standardizing work operations. And standardizing work operations can benefit your facility drastically.
The advantages of standardizing work tasks include gaining a better understanding of which tasks need your focus and improvement, which becomes increasingly helpful for training new staff and measuring the success of your current employees. Also, it can help you be fully transparent with your team about your expectations. Lastly, it will help increase efficiency.
Brammer emphasizes the importance of counting, collecting, and measuring data to standardize daily work tasks. And as he puts it quite simply, you must do the math. You can achieve this by counting and measuring the percentage of time and effort the tasks in your facility yield. Then, once you can distinguish which functions require the most effort or consume the most time, you can start setting realistic goals.
Use Practical Tools to Improve Problem Solving
Once you begin setting yourself up for success with different organization strategies, you will be better prepared to define and solve problems in your facility. Overall, problems within a facility are inevitable. And the best way to handle an issue is to treat it as an opportunity for improvement. Here are some tools Brammer suggests for improved problem-solving within a lab animal facility.
Fishbone Diagram
Brammer recommends using a fishbone diagram to brainstorm the causes of a problem, and the effect, to create the best solution. The advantage to a tool like this is it can objectify the issue, identify it–and take the burden off team members. Rather than arguing, you can focus on finding a solution.
The advantage of working together as a team to solve problems is that it allows people who closely know the problem to offer solutions. Then, it becomes management’s responsibility to help resolve the issue.
The Eisenhower Matrix
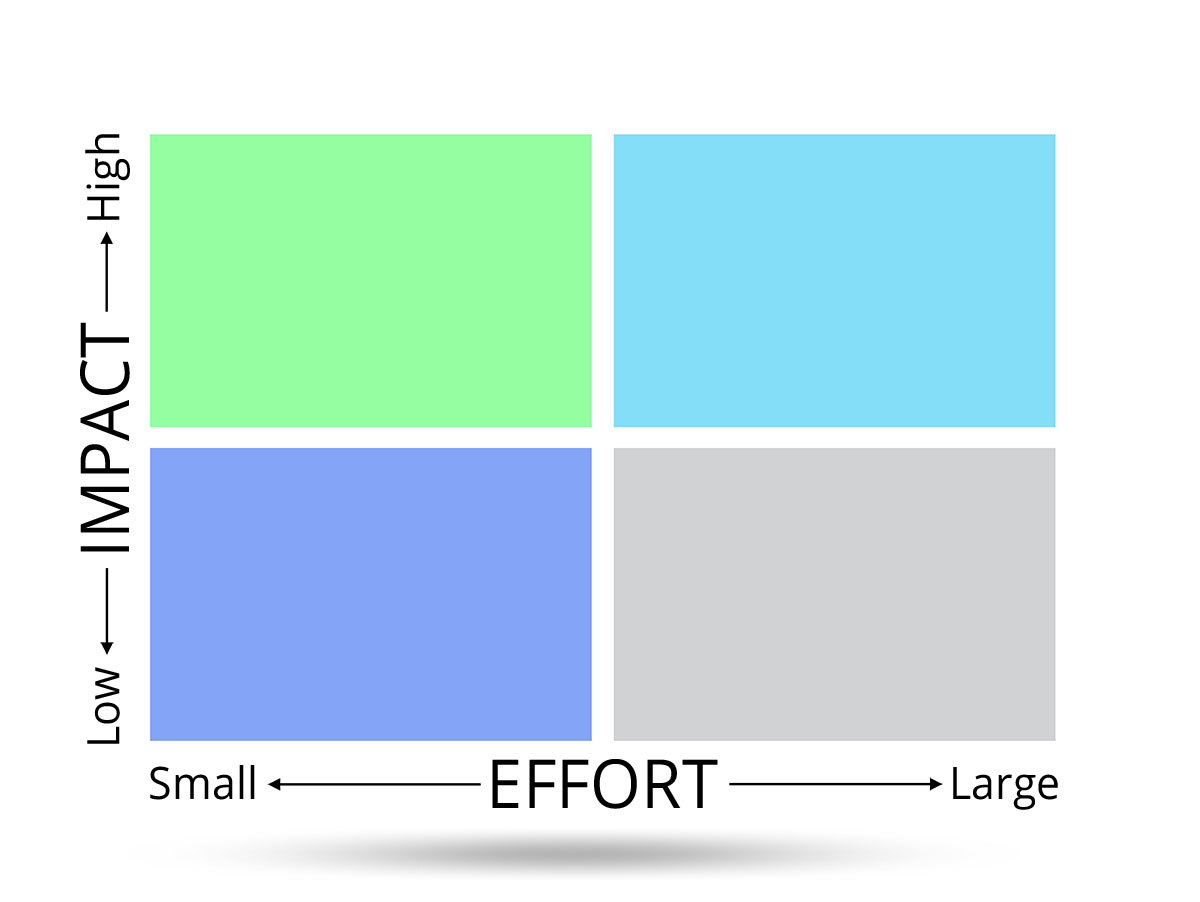
Brammer explains that the Eisenhower Matrix is the most crucial part of the fishbone diagram exercise. It can help you measure the expected effort of a task from small to large, and the impact from low to high.
By creating an Eisenhower Matrix, you can systematically understand and determine the urgency and importance of resolving any given problem. For example, if an issue ends up in the top left box, it’s vital to work through it first.
More From Our Webinar: Minimizing Micro-Frustrations
Once your facility is more organized and standardized, you will begin to see improvements in your facility. Your facility will become more orderly, quiet, clean, focused, and peaceful. Furthermore, you will minimize micro-frustrations.
Micro-frustrations are little annoyances in the workplace. But the effect they have on employee satisfaction is not so little. These small disturbances build up and create dissatisfaction among team members. According to Brammer, by fostering an organized, standardized work environment, you can significantly reduce micro-frustrations in the workplace.
Watch Our Webinar Now to Learn More
If you want to learn more about continuous improvement in the lab animal field from Dr. Brammer, a recording of our webinar is available now.